How can queries improve your performance
- Flora Mengue
- May 29, 2022
- 2 min read
Updated: Jan 11, 2023
Queries are used to view data to answer business questions.
Most ERP systems allow you to retrieve or display data from your database in several ways: through generic reports and dashboards already configured in the system or through custom filters, reports and dashboards.

Managers or professionals often look at data to measure performance or answer specific business questions. But more importantly, by looking at this data, we can better position ourselves against a goal: are we still aligned with it?
When we look a little deeper, we find positive gaps or problems.
Identifying and solving problems
Using queries helped me tremendously when I was a production planner for a small manufacturing company that had just hired me. I used generic reports to control inventory and track orders. I was also creating BAQs (Business Activity Queries). The company's ERP system was easy to use to create queries.
I remember a situation where I wanted a custom report with specific criteria. After creating this report, I initially thought that my report was not well done with the results. But when I asked my boss and the IT manager for input, we quickly realized there were anomalies in the system. These were old orders that had been delivered but not invoiced to customers. This information was also in the generic reports but in less detail.
Not everyone in the company was happy about this news, but it made us aware of the problem. As a result, my custom report became a control tool for the finance department and was integrated into their procedures.
I created several other queries to ensure the reliability of our data. For example, the query on completed/closed work orders versus picking transactions allowed us to keep an eye on inventory for missing transactions. For example, not closing a work order without deducting stock.
Queries (Select queries in this context) are excellent tools to read the information in the system, depending on the objectives and questions we want to answer.
Indeed, technologies are there to make our lives easier. And in the business world, intelligent systems and technologies are there to make companies more efficient. But if you have unreliable data or don't consider data in your decision-making, you can miss out on a lot.
In addition, the foundation of lean management is waste reduction. Using technology can also be used to identify or reduce this waste.
As a bonus, by waste, we mean activities (perhaps necessary) that do not add value to the customer and for which the customer is not willing to pay.
There are seven types of waste in the traditional Lean approach, plus an eighth that is human-centered. Finally, the eighth will encompass all resources where creativity is lost.
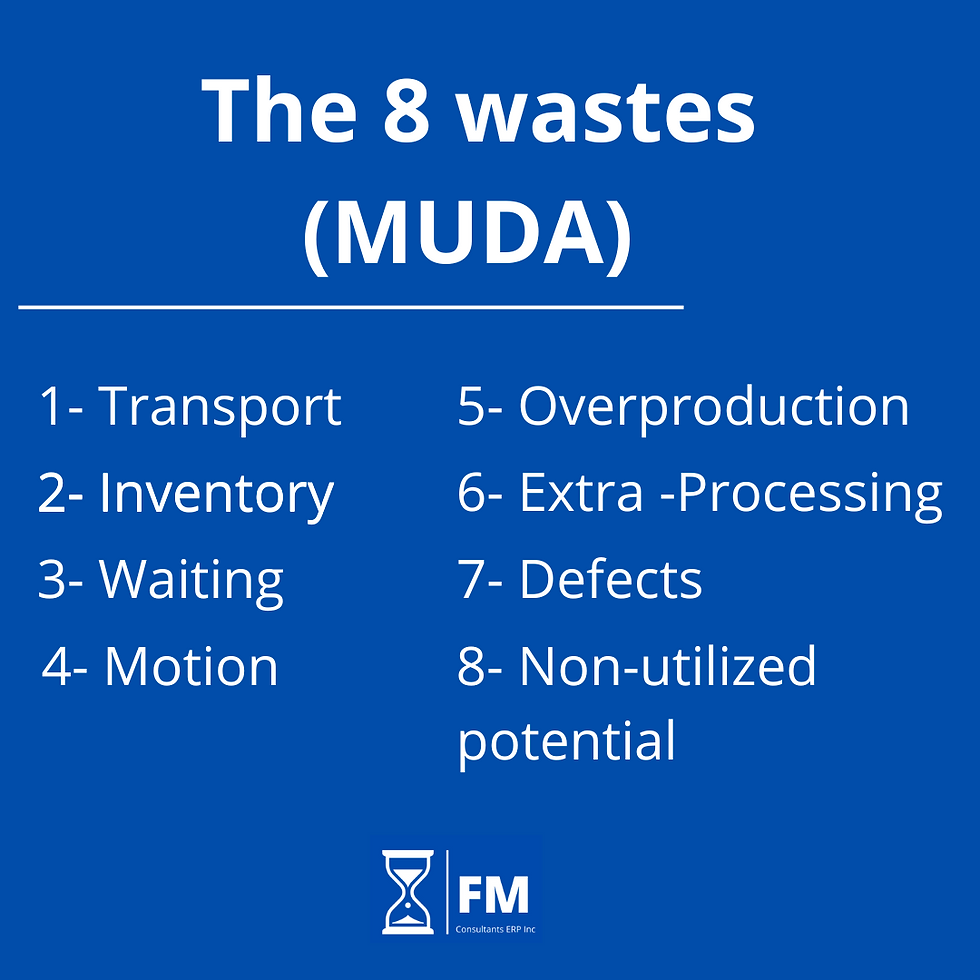
When looking at data, making hasty decisions, such as punishing or reprimanding resources, is very tempting. But the best attitude is understanding what the data means; what is the data telling us? Then, what can we do to improve outcomes as a team?
Did you like this article? Feel free to subscribe here.